前言
過去十年來在工業4.0浪潮下,促使工廠向智慧化轉型發展。面對工廠面臨勞動力短缺和長久以來產線機台不預期停機損失影響,計畫團隊研發了眾智式學習技術實現高準確度- 低誤警率的故障預診斷應用,以及AI泛用取物技術克服AI模型訓練需要大量高品質標記資料的瓶頸。技術不但分別獲得2017年全球百大科技研發獎和2022年CES展創新獎,也成功落地應用在半導體、金屬加工等產業,並技轉給達明、帆宣等科技大廠,讓科研成果嘉惠更多台灣製造業業者。
精彩內容
1.台灣製造業智慧化轉型需求與挑戰 2.深度學習人工智慧突破技術瓶頸 3.技術榮獲國際大獎肯定 帶領台灣產業轉型升級 • 故障預診斷技術榮獲全球百大科技研發獎 • AI泛用取物技術榮獲CES展創新獎
|
台灣製造業智慧化轉型需求與挑戰
政府力推數位轉型,將成未來經濟發展重要基盤與動能,領域知識、人工智慧、大數據,將是產業數位轉型的要件。以下說明產業面臨的問題與挑戰:
勞動力短缺問題
過去許多產業,如製造業、倉儲物流業,在面臨勞力短缺的問題時,可透過導入機器手臂執行重複性的工作來補足勞力需求。然而,近年來,在產品少量多樣的趨勢下,要將自動化技術擴散到中小企業主要會面臨兩大問題:1.客製自動化機構及演算法耗時耗力,每件新品至少都需1-2星期以上的調整測試時間,無法因應產業少量多樣的產品趨勢;2.導入成本大幅增加,除了硬體相關成本外,每件新品皆需客製化演算法及相關的維護成本;因此單純的自動化已逐漸無法滿足產業需求。若採用現有常見的主流AI技術來解決上述問題,在實際應用落地上,仍需要面對三個常見重大挑戰: 1. 訓練資料取得與標記成本太高;2.訓練好的模型對於和訓練資料有顯著差異的測試資料,辨識正確率大幅下降;3.缺乏泛用性,使得新物品加入時須重新學習。
產線機台不預期停機損失影響
台灣半導體產業被譽為「護國神山」,其產線機台全年24小時不停運作,僅一年進行一次歲修。若良率下降,影響將連鎖且持續,因此機台穩定運行對良率和股價至關重要,不僅需先進製程,更要精準控制微小的良率變動。然而,目前業界仍主要依靠工程師經驗進行異常判斷,查找問題平均需4~5天,嚴重影響產能。雖然故障預測技術已發展十餘年,但準確度不足,難以實現全面應用,故障排查仍然依賴人力判斷,影響了生產效率和產品品質。
深度學習人工智慧突破技術瓶頸
全球製造業越來越重視「以人為本」的製造模式,從德國的工業4.0到美國的製造業回流政策,皆致力於將人員角色從機械操作員轉變為生產流程的決策者和管理者,透過智慧製造和人機協作來提升生產力並優化生產流程。以下我們介紹如何利用人工智慧來實現機台故障預診斷與AI機器手臂泛用取物。
機台故障預診斷
IBM研究報告顯示,83%的資訊長認為設備維護和資產分析最佳化是提升企業競爭力的關鍵。導入故障預診斷技術可帶來顯著效益,包括10倍投資回報率(ROI)、降低20%~25%維護成本、減少70%~5%意外停機,並提高20%~25%生產力,充分展現產線設備穩定性對製造業競爭力的重要性。面對專業人力短缺、市場波動及客製化需求等挑戰,全球製造業積極引入巨量資料分析技術,以提升產線診斷,降低設備突發故障風險。工研院研發的「半導體機台故障預診斷系統」正是基於此概念,為提升產業競爭力而誕生。
以光電工廠的磊晶製程機台為例,故障預診斷系統可預測質量流量控制器(MFC)和微粒過濾器(PF)的故障機率與剩餘壽命,從而合理安排零件更換和維修時程。提前預知並排除異常事件,不僅減少突發故障查修壓力,還提升產線工程師效率,促進工作與生活平衡,讓工程師專注於創新研發,創造更高附加價值。然而在實務應用上,預診斷系統要能夠被信任的重點在於:高準確度和低誤警報率,避免當放羊的小孩,造成真正機台異常時反被忽略,這也是我們開發這一套眾智式學習演算法,想要追求的目標(如圖1)。
回顧「半導體機台故障預診斷系統」的研發過程,完成這套系統有兩大關鍵。
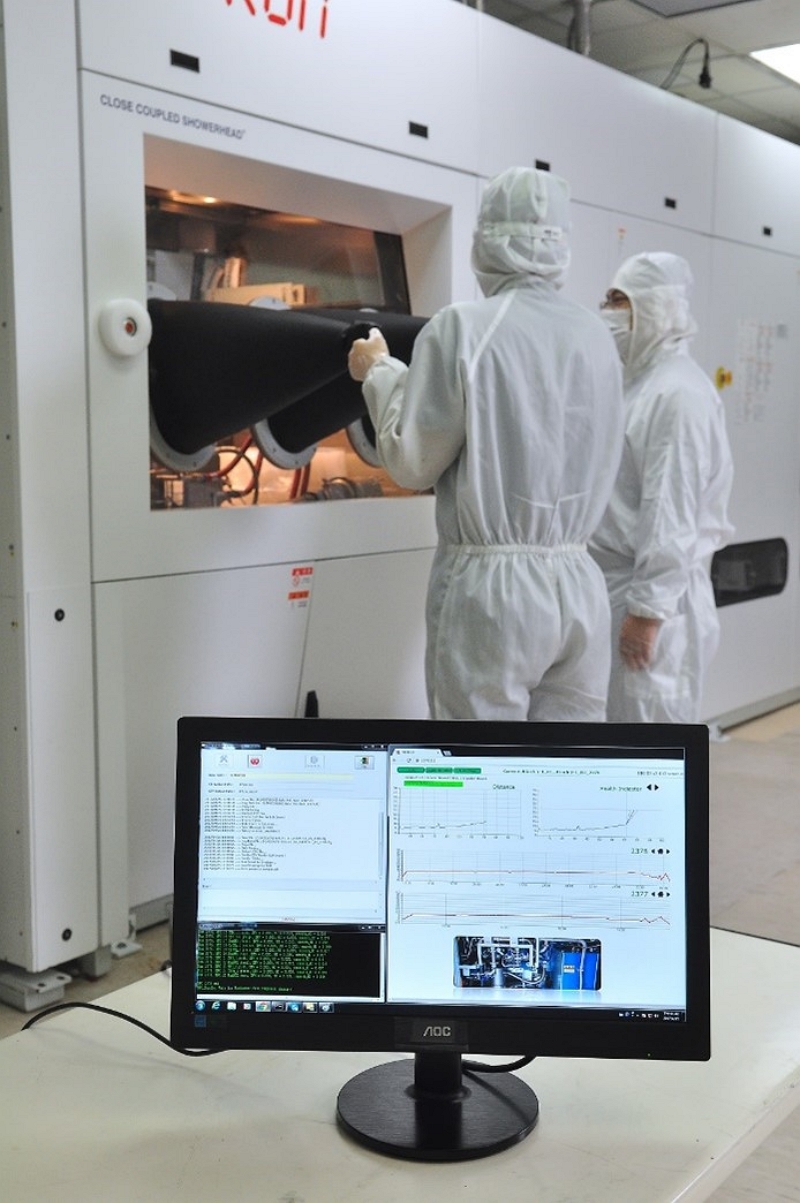
圖1 運行於光電半導體產線的故障預診斷軟體
關鍵1》蒐集準確資料並萃取關鍵參數
半導體產線的資料參數,多達400、500種,要從中找到真正影響機台健康的參數,是研發這套系統的第一件關卡。在特徵參數擷取階段結合機台/零件的規格特性,除可提升特徵參數的鑑別度,更可維持預測模型的通用性,提升系統之可攜性。在LED MOCVD零件故障預測中,採用process segmentation技術來擷取出反映各種零件老化程度的關鍵製程區段,並在該區段中取出特徵參數。為此,整合光、機、電與資訊軟體等領域的研發團隊,經過反覆驗證與測試,順利找出能反映機台設備健康的關鍵參數。
關鍵2》眾智式學習預測技術
在找到關鍵參數後,研究團隊建立了資料分析模型,並突破傳統單一「英雄式」演算法,整合多種先進機器學習算法形成「眾智式學習預測分析模型」(如圖2),大幅提升預測準確度。特別是若預測準確度不足,頻繁的誤警報會干擾產線工程師並影響效率。工研院研發的眾智式學習預測分析技術將準確率提升至95%以上,顯著減少誤警報,助益產線穩定運行。ITRI PHM的技術創新有如下兩點:
- 具高精度:可精確預測設備零件在4小時(或客戶指定時間)內可能發生的故障,為技術工程師爭取足夠的處理時間,減少突發故障帶來的損失,滿足廠商需求。這使得生產排程、物料準備和人力調配更為簡便,有效提升設備利用率,並降低產品質量下降的風險。
- 可擴展性:ITRI研發的PHM技術具備高度擴展性,適用於多個領域。除了半導體設備外,還能應用於機械加工和電力設備的故障預測,有效降低故障不確定性。目前,該技術已在國內半導體公司產線上成功應用,實現異常現象的準確預測。
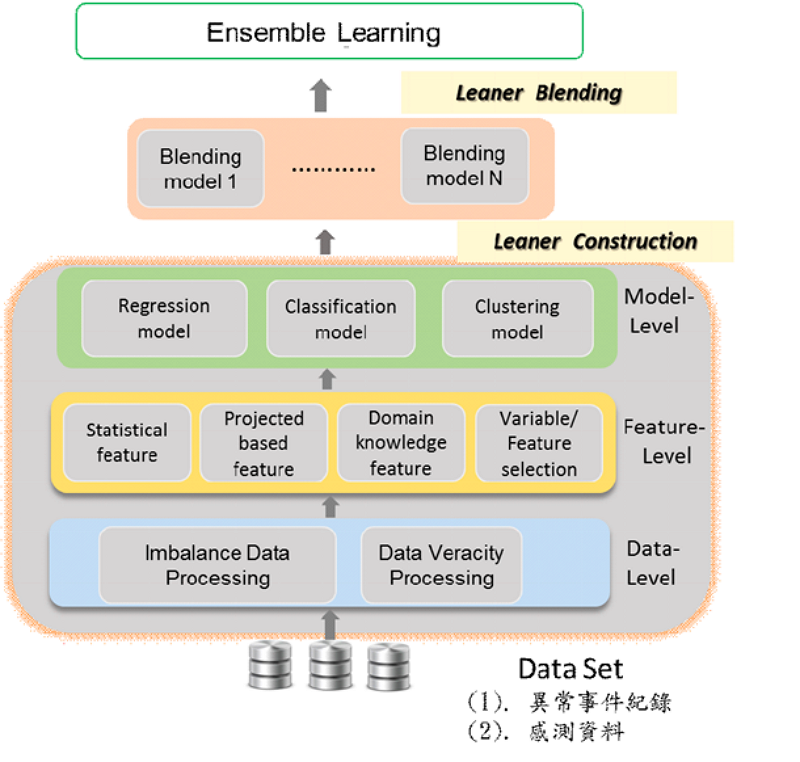
圖2 眾智式學習預測技術
此故障預診斷軟體功能包括
1. 零件剩餘壽命預測技術
透過挖掘隱藏在數據中的有用資訊,開發出能動態整合歷史故障模型與老化趨勢模型的技術,利用歷史數據與測試數據的變化趨勢來預測零件剩餘壽命,預測準確度超過92%,與國際大廠Applied Materials並駕齊驅,達到國際領先水準。
2. 人/機/料異常現象診斷技術
結合零件精度規格,擷取控制器偏差的特徵參數,利用分群技術找出離群值群集,並透過專家回饋發現工程師和資料分析師過去未察覺的異常。該技術涵蓋製程機台、感測資料、資料傳輸、人為疏失、原料不足等異常情況,解決巨量資料分析中的data veracity問題。此系統遵循可擴充的整體式學習框架,整合SOM、Multivariate SPC、kNN及基於領域知識的規則模型,構建整體式異常診斷技術。
基於自動生成高度擬真RGB-D影像訓練資料之AI機器手臂泛用取物點偵測技術
「基於自動生成高度擬真RGB-D影像訓練資料之AI機器手臂泛用取物點偵測技術」解決將AI導入實際應用所面臨的上述重大挑戰。透過結合產線模擬上之相關模擬器,以AI的角度切入,研發自動擬真標記資料產生相關技術,克服AI神經網路訓練需要大量高品質標記資料的瓶頸,讓取物演算法具備高度的泛用性,在面臨不同樣式的產品時,皆能適用。
此外,在取物應用的導入成本上,過去除了機器手臂、3D攝影機的硬體成本外,還需要演算法軟體設計及維護成本,整個解決方案加起來大多大於100萬以上,這對於中小企業來說,成本太高,以至於導入意願不大。因此,本技術的另一大目標就是要能夠將泛用取物技術內建在機器手臂中,讓企業在導入機器手臂的同時,手臂本身就具備泛用取物功能,除了增加機器手臂商的附加價值外,也可以增加企業導入的意願,加速技術的擴散。根據上述策略目標,我們於與國內第一大(市占率全球第二)的協作型機器手臂商達明機器人合作,成功將技術技轉給達明機器人,大幅減少中小企業的導入成本,並成功將此技術擴散到不同產業,如倉儲物流業(長呈五金)、機器人系統整合商(台朔重工)、與金屬加工業(英發實業)。
技術突破點包含以下三項:
1. 高度擬真模擬資料產生與自動資料標記技術
以過去導入自動化技術產線模擬上使用的模擬器為基礎,利用模擬器能夠模擬物品受到力量,如本身重力、摩擦力等,的物理行為能力,來自動隨機產生取物應用上所有可能遇到的場景,並結合高擬真的渲染(Render)引擎Blender,讓產生的模擬場景接近真實場景,創造一個接近真實世界的模擬環境。
根據所建置的擬真模擬環境,我們開發2個場域常見的取物場景產生機制:1. 散亂堆疊、2. 緊密擺放,讓我們可以快速產生大量且具多樣性的擬真取物場景。下圖3為分別為兩個隨機產生的擬真場景。
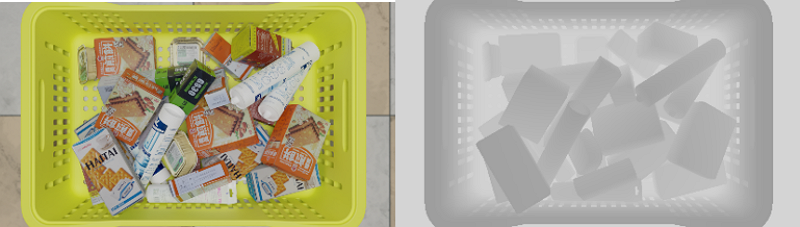
散亂堆疊
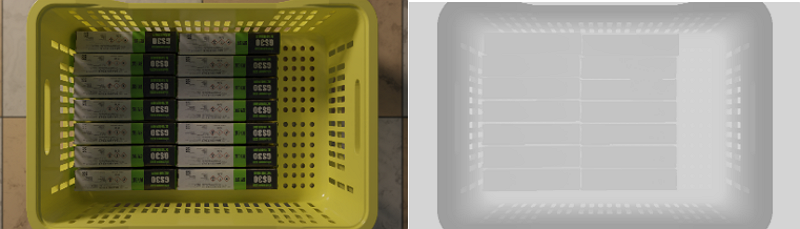
緊密擺放
圖3 在不同模擬光源下所產生的RGB與深度擬真影像
在資料標記上,本團隊萃取並分析模擬器在場景產生模擬過程中的相關訊息,如物件座標、姿態等,自動產生符合取物應用所需之標記資料,並開發1.高精準度未遮蔽物件分割自動標記、2. 取物點優劣自動標記技術,來自動化的產生AI所需之標記資料。
2. Domain Randomization技術
本團隊綜合與多家廠商洽談與合作的經驗,在眾多的擾動因子中,經過反覆地進行模擬資料產生、神經網路訓練、與實體場景推論測試等步驟,歸納出6大關鍵擾動因子,並分別透過模擬器與影像後處理產生擴增資料集,除了克服環境變異外,也克服模擬資料與真實資料間的差異(Sim-to-Real Gap),讓取物效能具備高度的強健性(robustness)。
3.基於RGB-D影像之AI泛用未遮蔽物品取物點偵測技術
結合本團隊所開發之深度圖泛用取物點偵測技術 Fast Suction Quality Network (Fast SQNet) 與彩色RGB泛用未遮蔽物件分割技術,並搭配增量學習(Incremental Learning)的訓練方式,在盡量維持推論速度下,持續提高泛用性。本技術搭配前述自動資料產生技術,可同時滿足實際取物應用所需之正確率、速度、以及泛用性。下圖4為透過本取物點偵測技術所預測之穩定取物點。
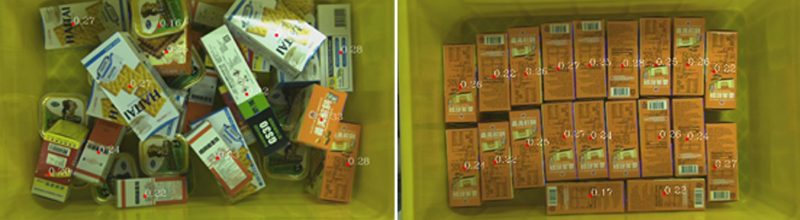
圖4 本技術應用於散亂堆疊與整齊擺放場景,輸出多個高品質候選穩定取物點及個別取物點品質分數
泛用取物技術,除了核心演算法本身外,技術團隊還對整個取物系統進行端到端(End-to-End)的優化,其中包括推論時間、GPU效能等,讓整體之取物成功率與推論速度皆達到實際場域應用需求,其整體之效能比較如下表所示。
表1 既有主流取物技術與本技術之比較
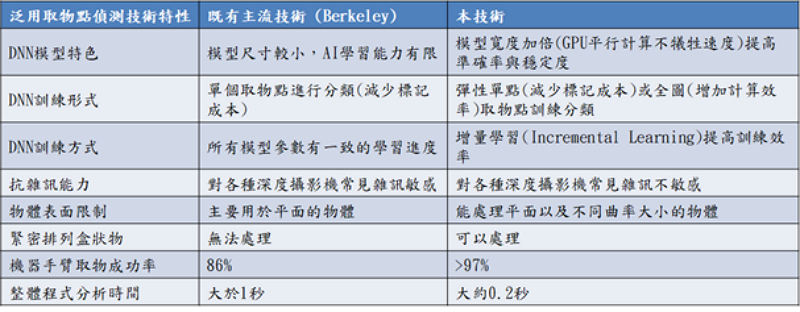
技術榮獲國際大獎肯定 帶領台灣產業轉型升級
技術榮獲國際大獎肯定
1. 故障預診斷技術-榮獲2017全球百大科技研發獎(R&D 100 Awards)
「半導體機台故障預診斷軟體」結合了人工智慧(AI)與機器學習,以巨量資料演算技術,分析機台所產生的製程資料,進行即時監看、預測並以視覺化資料呈現,讓產線管理者可以掌握設備的健康狀態,及早預測機台需要維修的時間點,減少產線因機台突然故障而必須停頓的風險,系統預測分析的準確率達95%以上。這套系統目前已技轉給國內多家光電半導體廠商,為國內產業邁向工業4.0的智慧製造時代,向前推進一大步,並獲得2017全球百大科技研發獎(R&D 100 Awards)的國際肯定(圖5)。
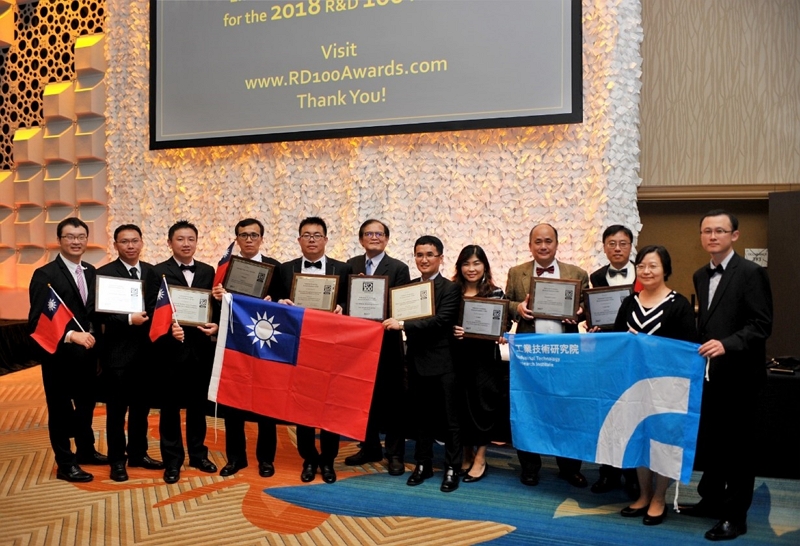
圖5 半導體機台故障預診斷軟體獲得全球百大科技研發獎
2. AI泛用取物技術-榮獲2022 CES(美國拉斯維加斯消費性電子展)創新獎
泛用取物技術整合達明機器手臂、感測中心開發的3D攝影機,打造全國第一台將3D智慧視覺感測與智慧取物做為標準配置的MIT智慧取物機器人,一舉奪下2022 CES(美國拉斯維加斯消費性電子展)創新獎,技術具備國際水準,並且能夠根據不同應用搭配合適的3D攝影機與機器手臂,整合上具備高度彈性,腦、眼、手能夠完美的結合,讓取物自動化應用落實於產業中。下圖6為2022 CES展參展實況。
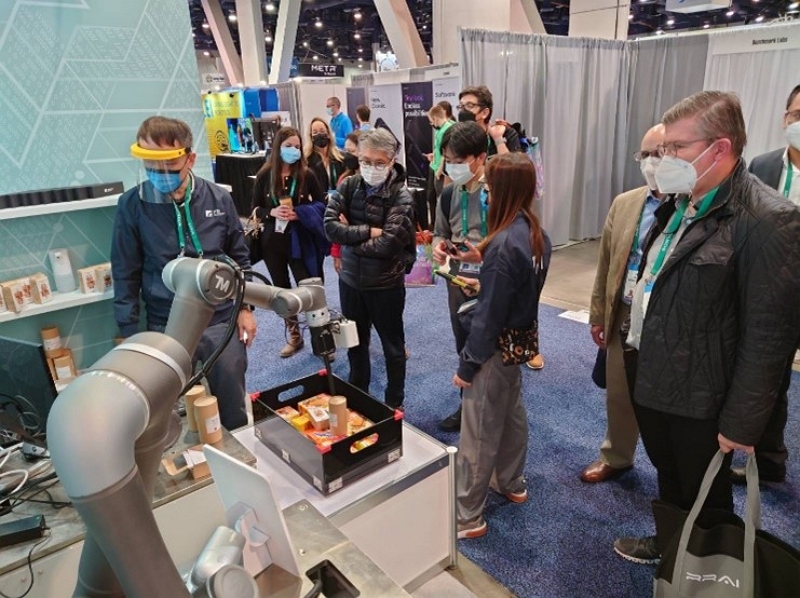
圖6 打造全國第一台MIT標準配置RGB-D AI泛用取物機器人榮獲2022 CES創新獎
產業落地應用案例
1. 達明機器人
成功將技術技轉給達明機器人,讓機器手臂本身就具備泛用取物功能,增加手臂的附加價值,改變手臂只能做單一重複性簡單工作的刻板印象,擴大機器手臂的產業應用,並大幅減少中小企業的導入成本,進而增加企業導入的意願。本技術結合達明機器人已成功導入全國第二大的五金百貨中盤商長呈五金進行自動撿貨。
2. 長呈五金
長呈五金為全國第二大的五金百貨中盤商,本泛用取物技術導入長呈五金水管料件撿料備貨應用上,透過供單系統,結合無人自動搬運車將客戶所需之水管料架運送到手臂前,再搭配所開發之泛用取物機器人根據供單系統的數量訊息進行撿貨;本技術的導入,讓長呈五金的水管物品撿貨系統得以自動化,除了補足勞力的需求外,也縮短出貨時間。
3. 台朔重工
台朔重工為倉儲物流業及製造業自動化具有代表性的系統整合商,此廠商已有一套成熟的倉儲物流系統,可以將使用者所需之料籃從倉儲系統中自動取出以便進行後續應用。然而,目前此系統再撿貨上仍需人工進行撿貨。本泛用取物技術補足台朔重工撿貨自動化的需求,讓整個倉儲物流系統可以全自動化。本技術結合供單系統與倉儲物流系統,共同於2021台北國際物流暨物聯網展展出,廠商反應熱烈,未來將共同推展落地應用。
4. 帆宣系統科技
協助帆宣轉型為巨量資料分析提供者,在光電半導體場域設備健康監控及剩餘壽命預估,實施最佳化維護策略,節省成本並提升競爭力,使臺灣成為全球光電半導體故障預診斷示範場域。並與帆宣既有的軟體人才共同推出產品Foresight PHM(圖7)。
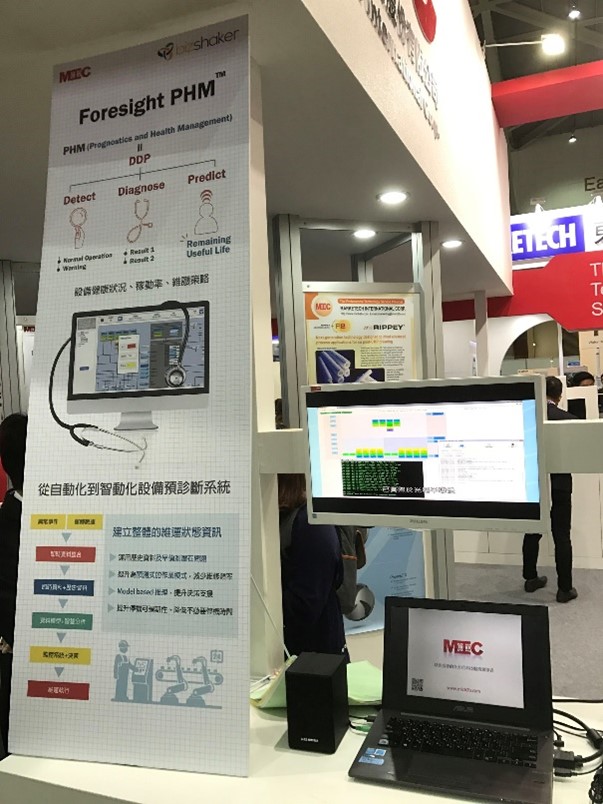
圖 7 帆宣在Semicon展示Foresight PHM
5. 華邦電子
建立光電產業垂直應用,水平擴散至半導體產業:透過在光電產業所建立的故障預診斷垂直應用示範案例,吸引記憶體大廠華邦電技轉故障預診斷核心技術,將產業應用效益水平擴散至記憶體產業(圖8)。
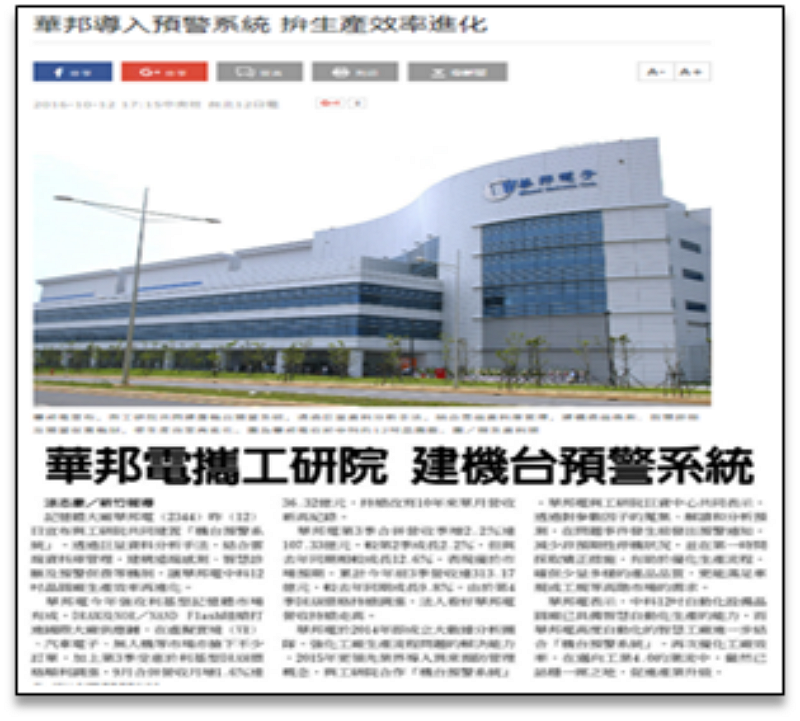
圖 8 華邦電攜工研院 建立機台預警系統報導 (資料來源:自由財經- 華邦電攜手工研院 建置「機台預警系統」)
結論
在工業4.0驅動搭配人工智慧技術的不斷精進下,智慧化轉型成為製造業因應勞動力短缺和產線機台停機損失的重要策略。工研院開發的AI泛用取物技術和眾智式學習故障預診斷應用,大幅解決AI模型訓練對大量高品質標記資料的需求,並以高準確度、低誤警率在故障預診斷中展現優勢。這些技術先後獲得2017年全球百大科技研發獎及2022年CES創新獎,並在半導體、金屬加工等產業成功應用,技轉於達明、帆宣等科技企業。展望未來,生成式AI技術將可望帶動新一波人工智慧在製造業的創新應用,如知識庫、影像生成、程式生成等,有助於增強工廠的彈性和競爭力,為台灣製造業開創新機遇並提升國際地位。